WEAV3D® partnered with Braskem, Clemson University, and Altair Engineering to design and prototype an innovative automotive beltline stiffener door component. Clemson previously converted an Acura MDX steel door assembly with carbon fiber PA6 organosheet; however, an alternative approach was needed to deliver a more cost-efficient solution that met performance requirements.
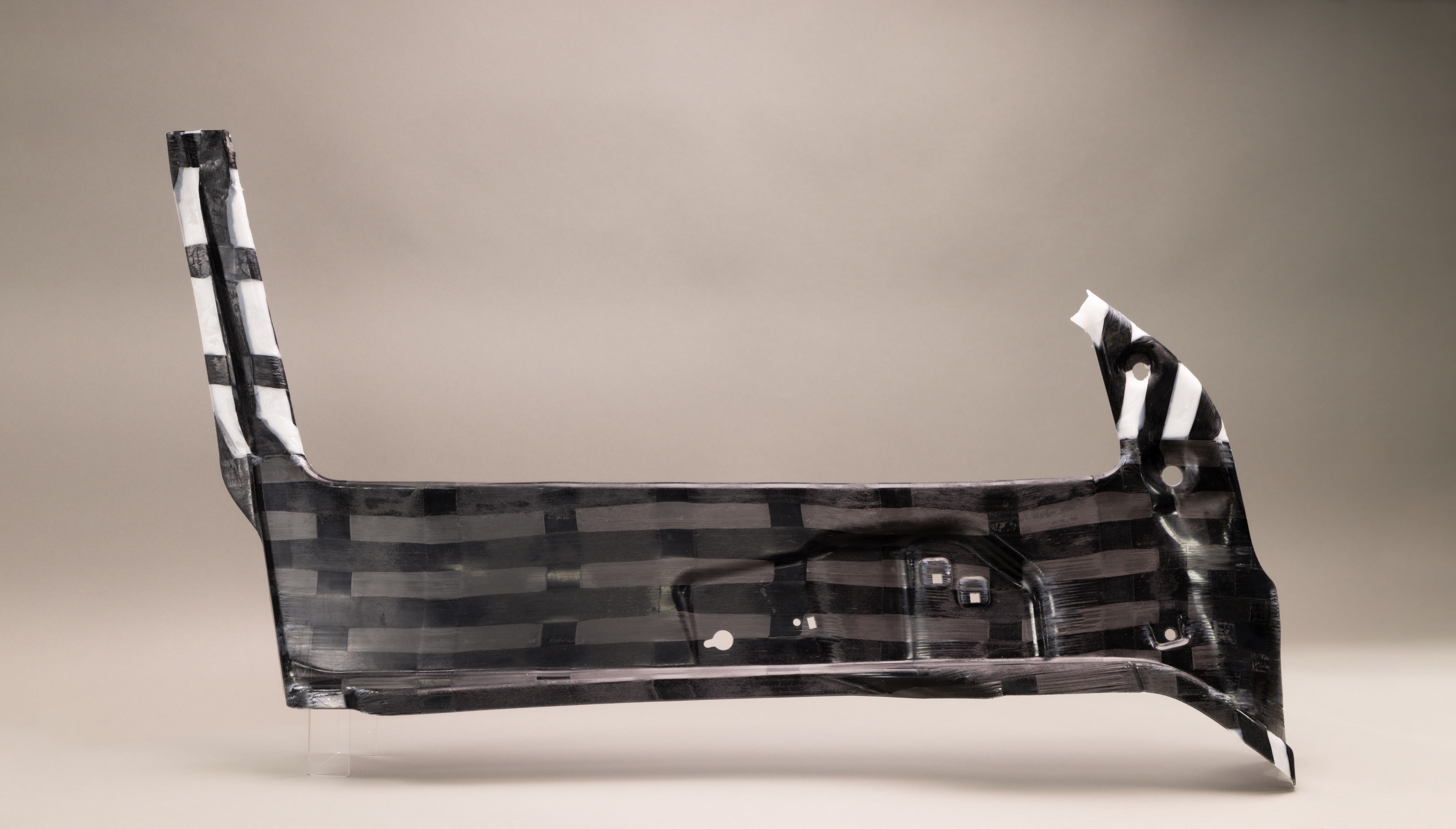
WEAV3D® partnered with Braskem, Clemson University, and Altair Engineering to design and prototype an innovative automotive beltline stiffener door component. Clemson previously converted an Acura MDX steel door assembly with carbon fiber PA6 organosheet; however, an alternative approach was needed to deliver a more cost-efficient solution that met performance requirements.
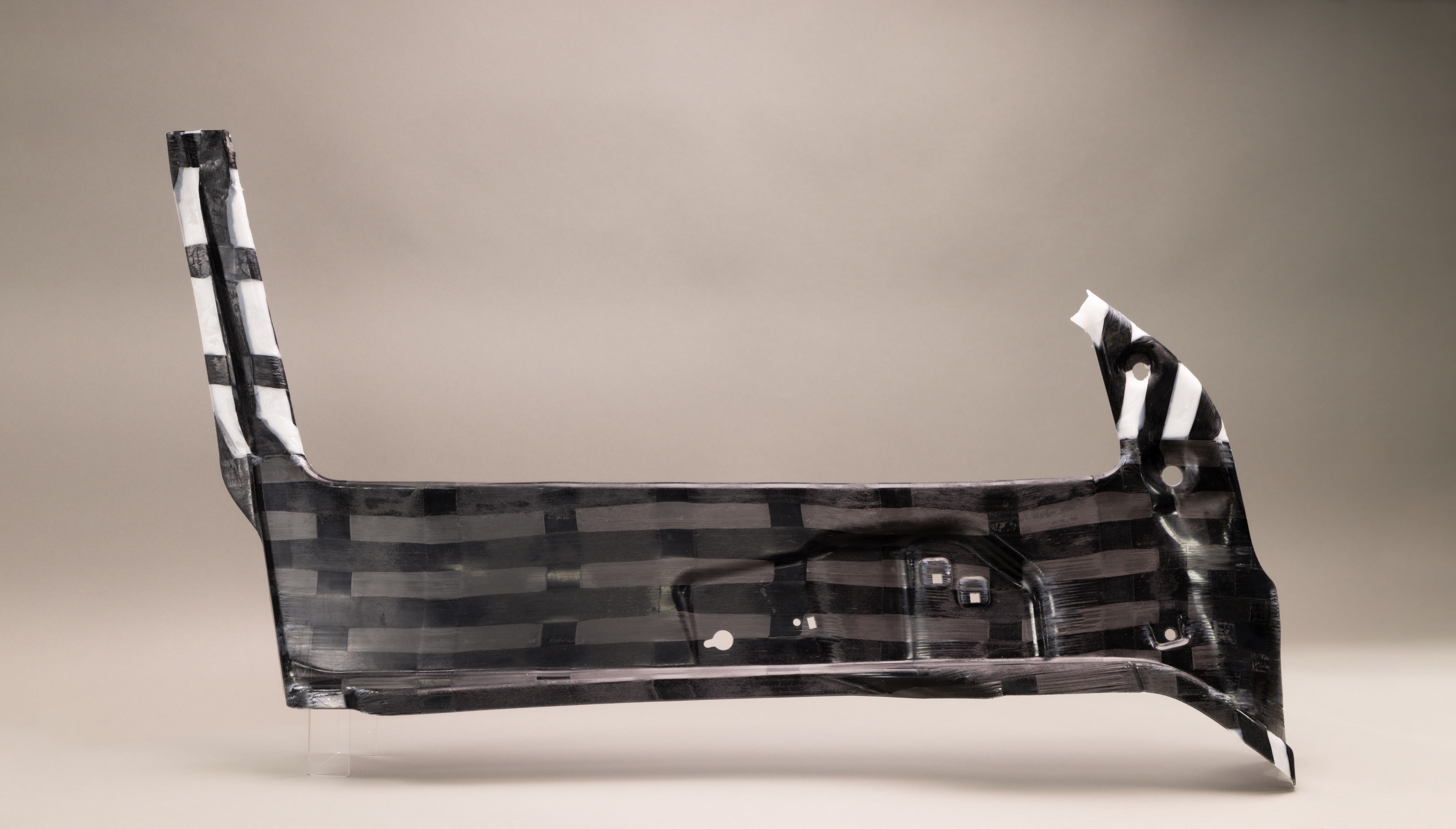
Process Overview
The innovative door component was manufactured from a topology-optimized WEAV3D® composite lattice comprising of glass- and carbon-fiber reinforced polypropylene UD tapes that were laminated to Braskem’s extruded polypropylene sheet via a continuous double belt press; then thermocompression molded in a matched-metal tool at the Clemson Composites Center; and finally, trimmed to dimension via a 5-axis waterjet.
Performance and Cost Benefits
The combination of WEAV3D® composite lattice with Braskem PP sheet reduced part weight by 23% and part cost by 50% relative to the CFPA6 organosheet baseline. By comparison, GFPP organosheet was 9% heavier and only 41% cheaper than the CFPA6 baseline.
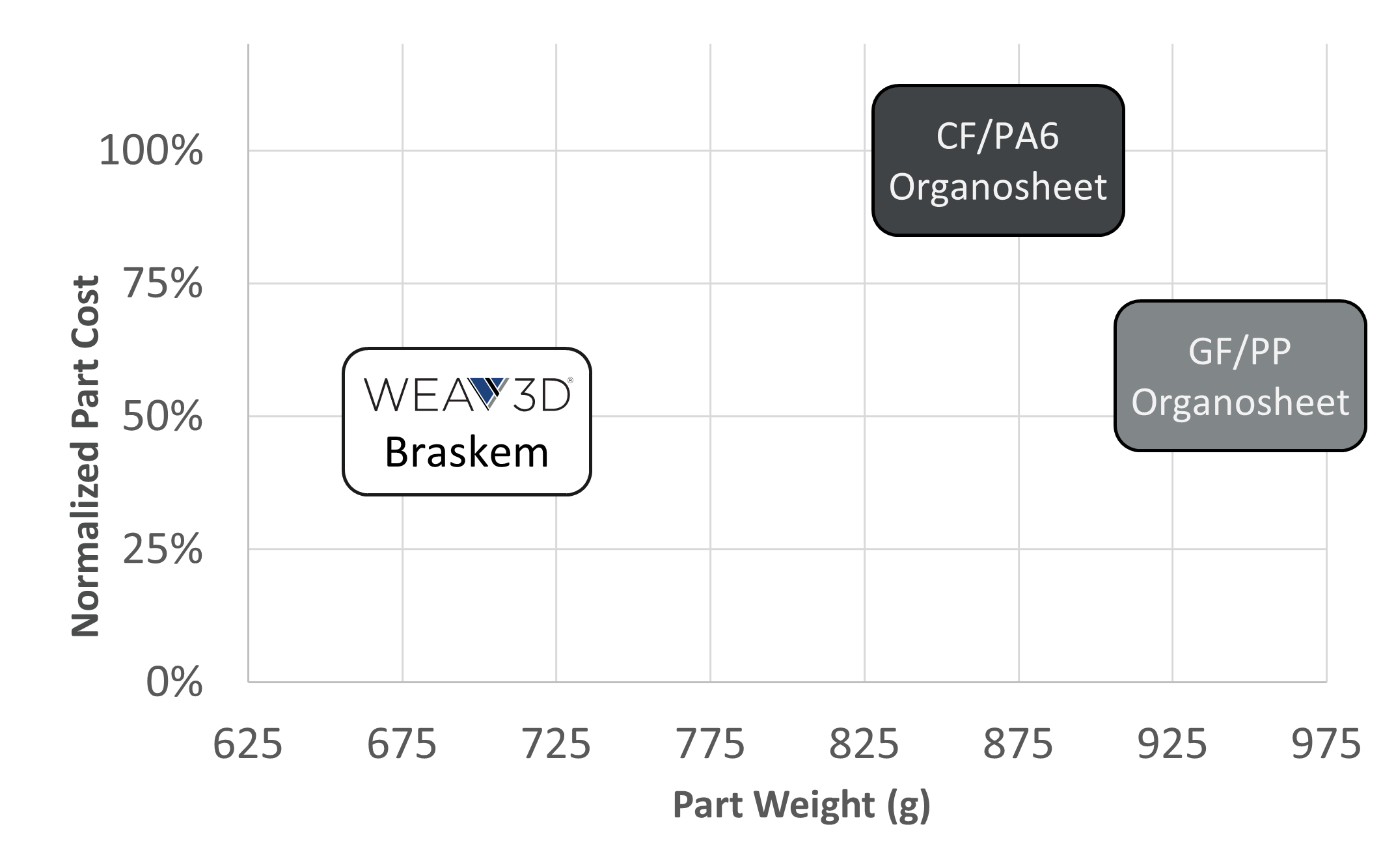
The combination of WEAV3D® composite lattice with Braskem PP sheet reduced part weight by 23% and part cost by 50% relative to the CFPA6 organosheet baseline. By comparison, GFPP organosheet was 9% heavier and only 41% cheaper than the CFPA6 baseline.
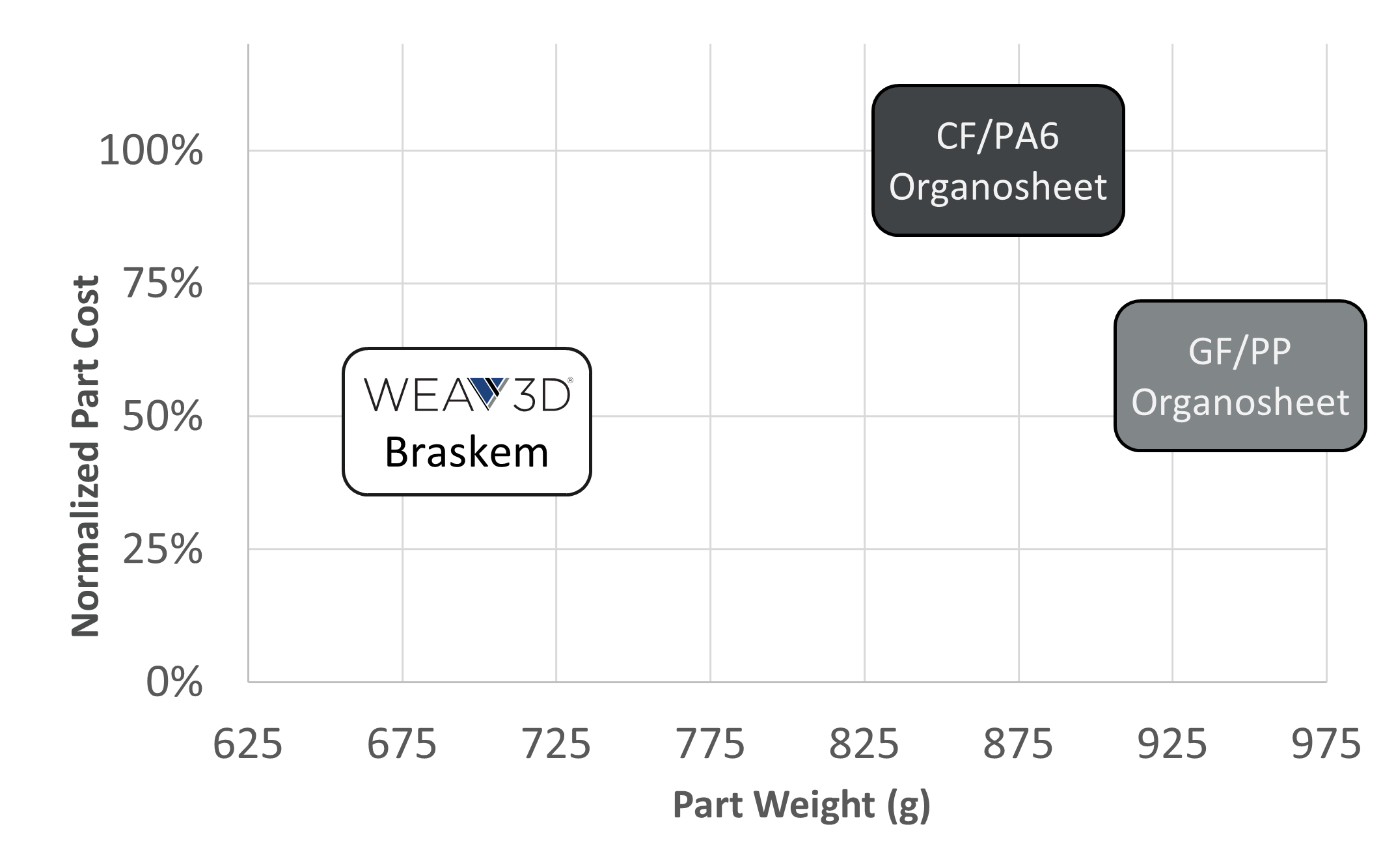
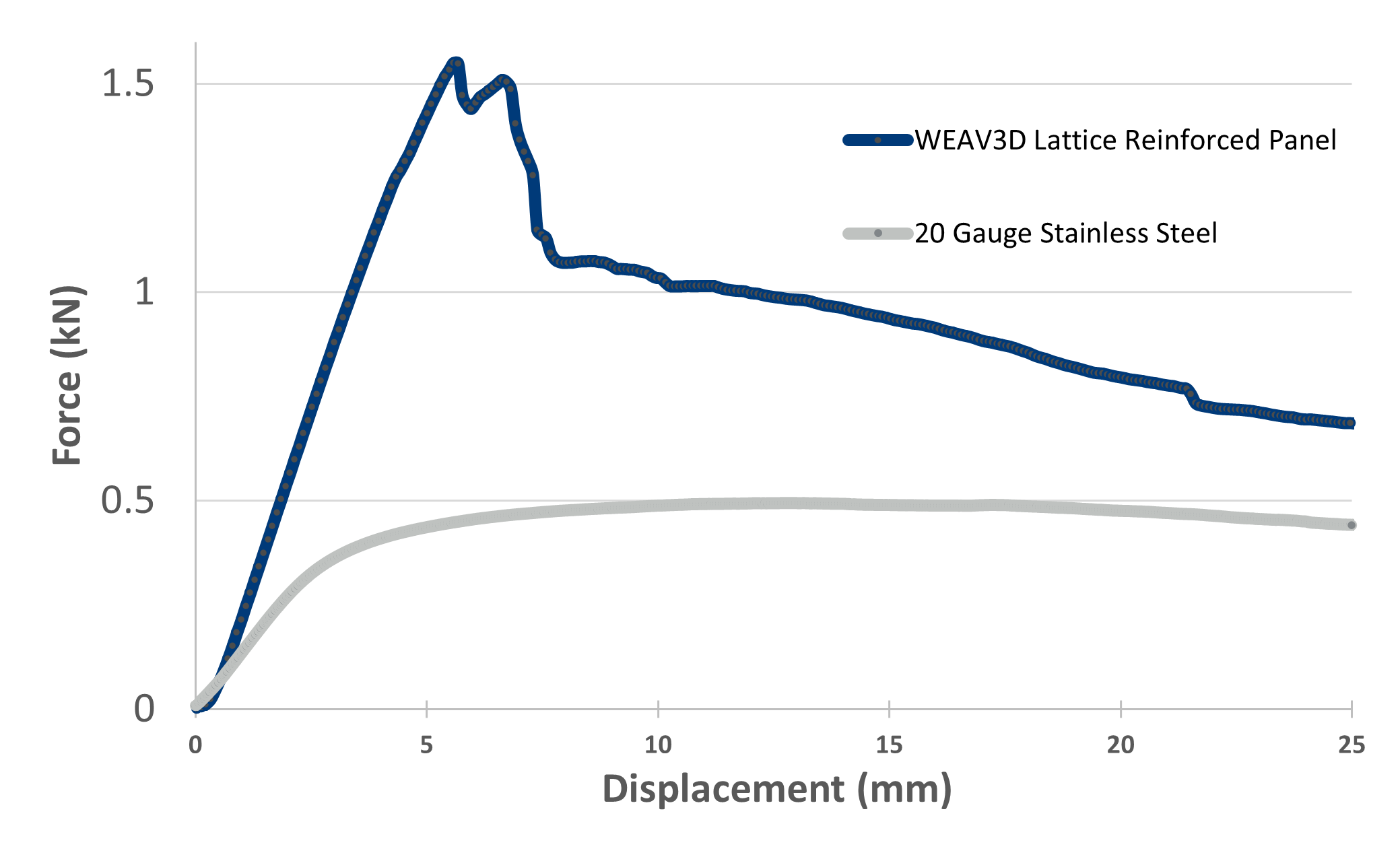
In flat panel testing, the WEAV3D® lattice reinforced design exhibited superior load capacity and bending stiffness compared to 20-gauge stainless steel, while achieving a 65% reduction in weight. Furthermore, the lattice reinforced plastic panels were able to both absorb more energy than steel and rebound back to its original shape following large deformations, while the steel remained permanently deformed. This translates to enhanced passenger safety as the door structure can recover from deformations that would otherwise trap a passenger in the vehicle.
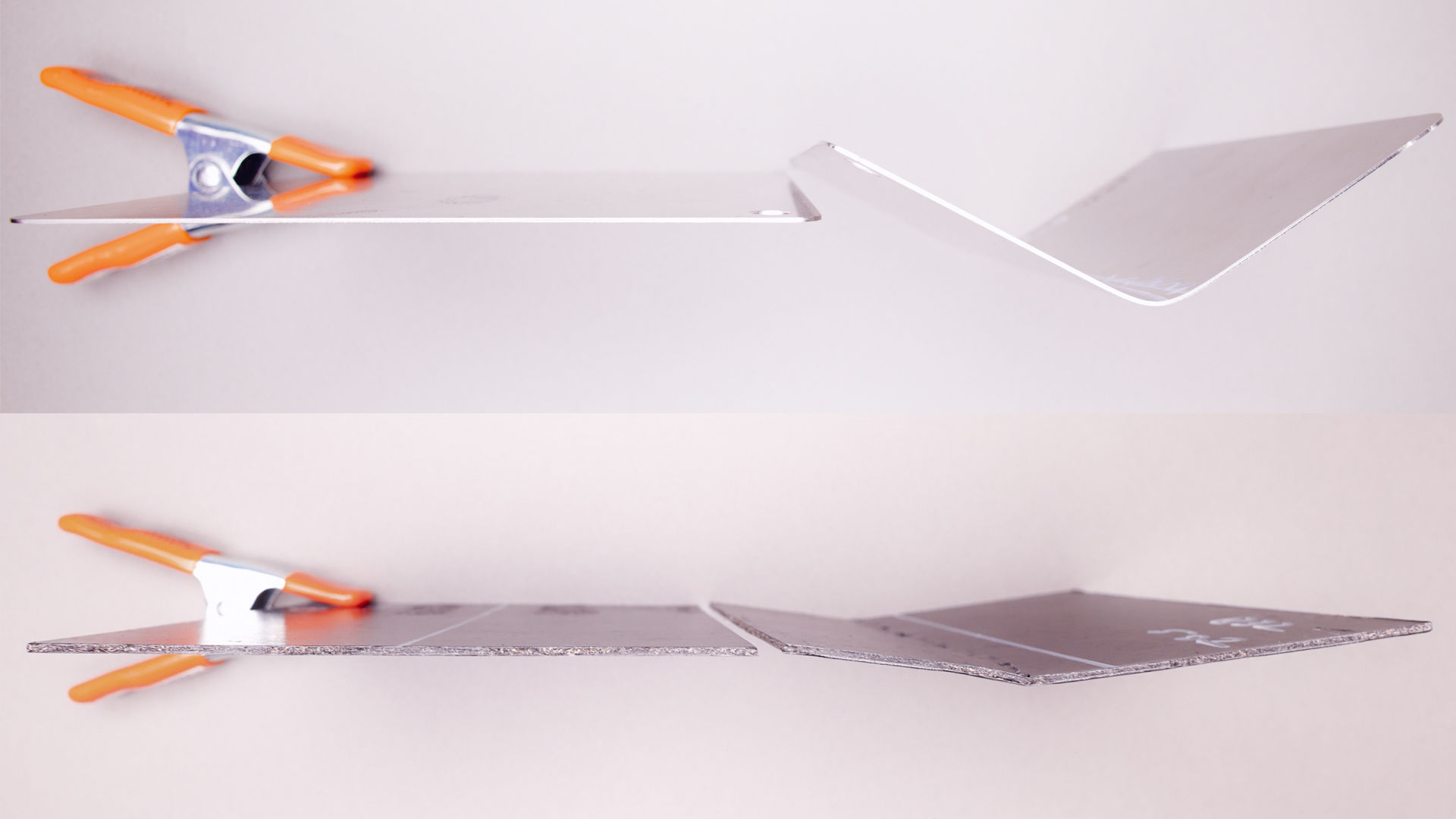
Sustainability
Switching from organosheet to the WEAV3D® lattice reinforced polypropylene design improved the material yield rate (final part weight divided by weight of input materials) from 25% to 45%, which when combined with the achieved mass reduction, resulted in a 63% reduction in trim scrap by weight.
The lattice reinforced beltline stiffener design combines two fiber reinforcements – glass and carbon fiber – with a monomaterial polypropylene polymer matrix and polypropylene sheet. This enables easy recycling via shredding and compounding of in-process trim scrap and end-of-life parts. Due to the efficient utilization of lattice reinforcement within this design, fiber only makes up 18% percent of the starting sheet by weight, which should enable regrind without requiring dilution with virgin polymer.
No volatile or hazardous chemicals are used in the lattice forming, lamination, or forming process. Implementation of film insert molding or mold-in-color as an alternative to painting also presents an opportunity to eliminate a major environmental hazard – the automotive paint booth. Not only do paints contain vapors and chemicals hazardous to workers, but colorants can also contain heavy metals that leech into the environment if not properly contained and disposed of, particularly during end-of-life recycling.
In Partnership With:
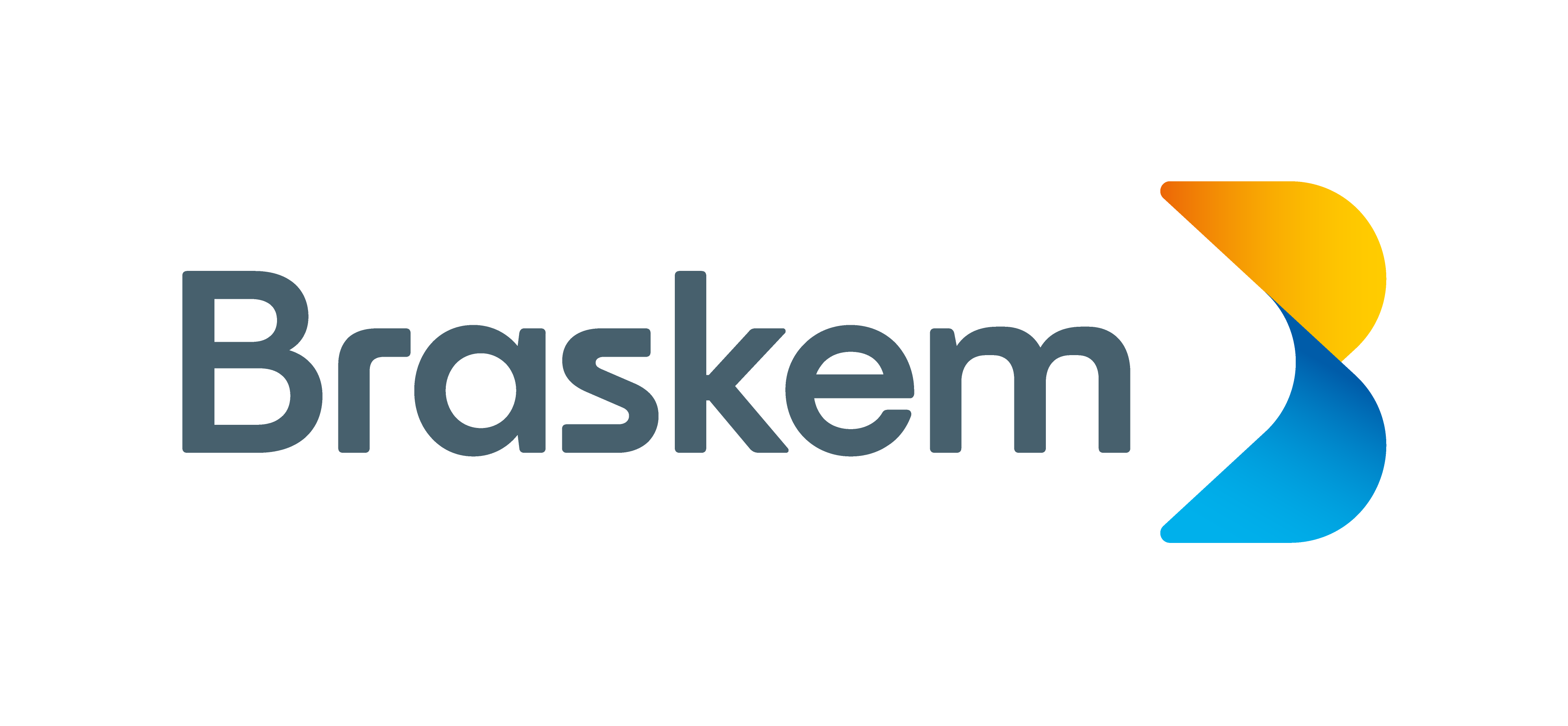
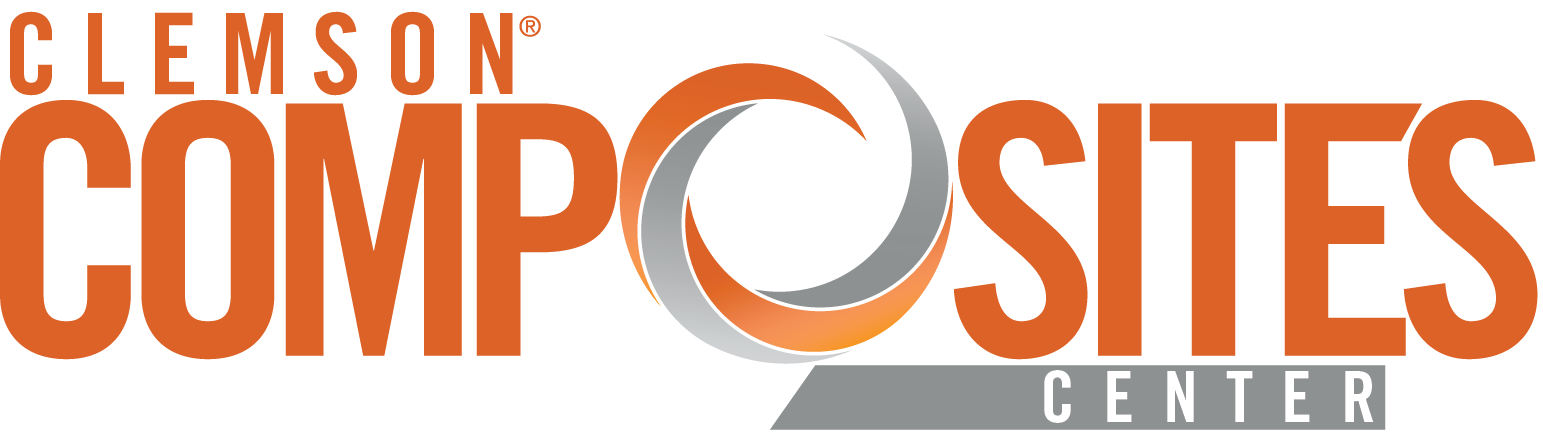
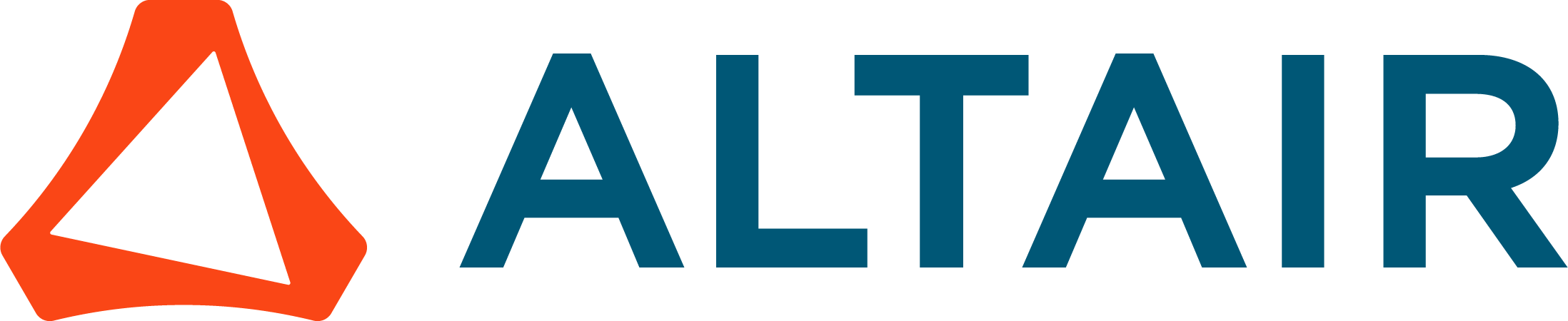
